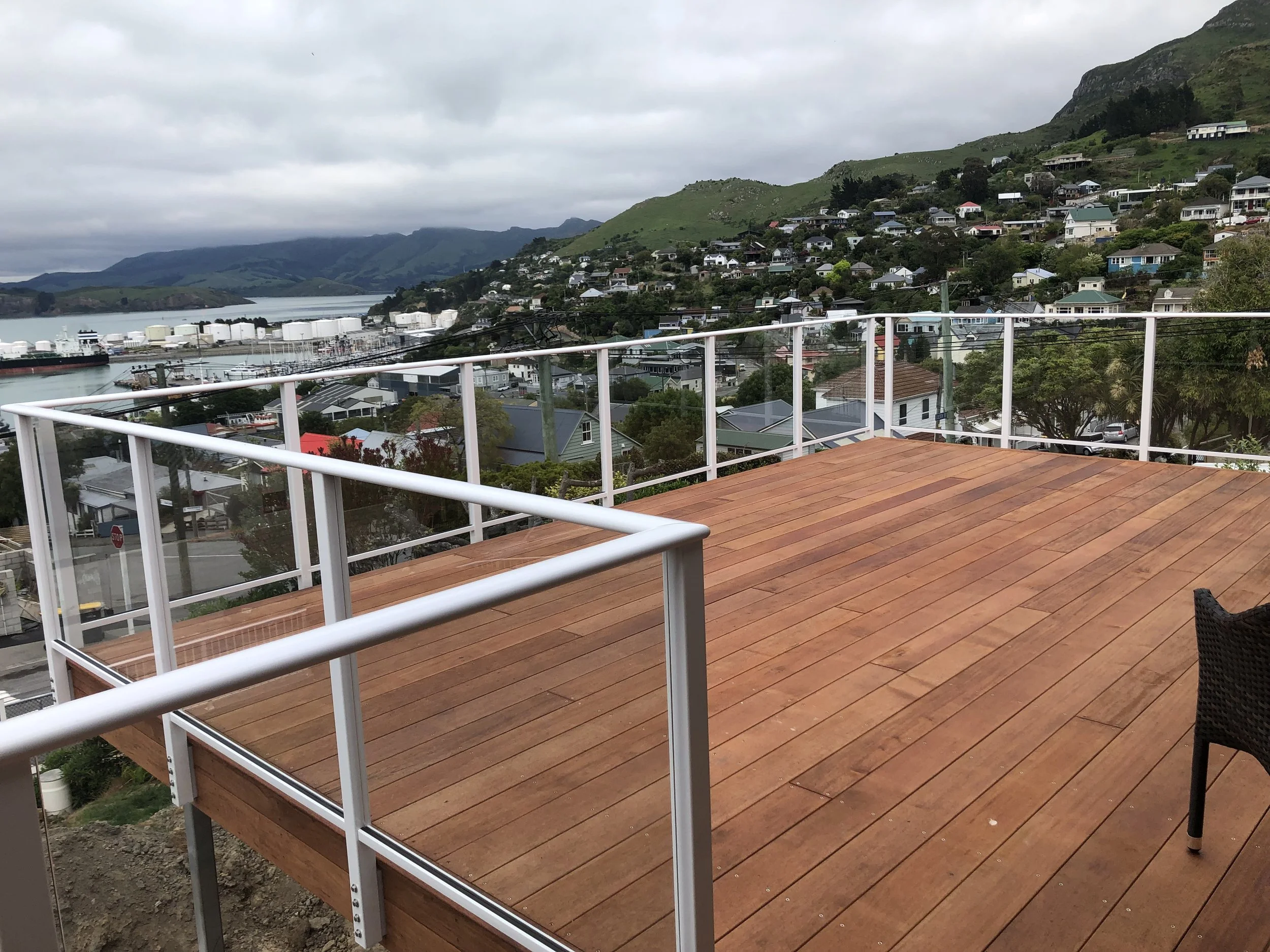
CASE STUDY
Port Hills Elevated Deck
Project overview
Our clients wanted to extend their existing decked area to create more outdoor living and capture views of the Lyttelton harbour.
The site was a hill section in Lyttelton and existing deck was an access to the house and was not facing the view. The proposed decking area was to be built facing the view. Due to the height of the decking being over 1.5m we engaged an Engineer and managed consents.
Vital stats
Construction of concrete foundation footing, erection of steelwork, construction of timber subfloor and lining of decking timber. Installation of glass balustrade.
BUDGET
$50,000*
SIZE
40m2
PROPERTY BUILT
1980s
DECK BUILD TIME
One month
Timeline of Works
Initial meeting with client
Site meeting with client to go over proposed decking area. Asked questions such as size of decking area, decking materials, balustrade style etc.
Engineering
Contacted Engineer and requested a fee proposal. Confirmed the client was happy to go head with the project based on the fee proposal. Arranged site meeting with the Engineer, to go over project and take a soil test. Engineer provided concept design for the proposed deck structure. Proposed decking plan was checked over by the client to confirm they were happy with the size and position of the deck area.
Consent
Complete Engineer’s plans and specifications were submitted to the Christchurch City Council to obtain a building consent exemption for small alterations.
Final costing and ordering of materials
Full job costing off consented plans was completed and accepted. A fixed price building contract was sent outlining the project details, including estimated start and completion dates. The job was confirmed by the client and an initial deposit was paid. Structural steel was ordered and the project start date was confirmed.
Set out and excavation
Set out of the concrete foundation was completed and excavation contractor excavated the area to allow for formwork to be installed.
Formwork and concrete
Premade shutters were installed and braced to footing plan provided by the Engineer. Reinforcing steel was installed and sections were tied in to existing house foundation with reinforcing rods and epoxy. Concrete levels were marked on formwork ready for concrete pour. Due to the section being sloped the footing level stepped to allow for this. Concrete was poured using a concrete pump and truck due to access issues.
Structural Steel
VIP was engaged to manufacture and help erect the structural steel. This was delivered to site by truck and erected in place using a Hiab. Sections of the steel were bolted to the preexisting house blockwork, fixed with epoxy rods. Due to the size of the structure, steel beams were made in smaller sections and site welded when in place.
Scaffolding
Scaffolding and safety nets were installed underneath the steel structure and handrails were erected. This allowed us to build the timber subfloor of the deck off the steel structure while being safe and complying with health and safety regulations.
Subfloor framing and decking
Installed timber joists at 400 centres as per Engineers plans, these were bolted directly to the steel structure with stainless steel coach bolts, along with a number of stainless steel nail plates. 140mm kwila decking was laid and fixed with stainless steel screws. All fixings were required to be stainless steel due to the site being in a sea spray zone.
Balustrade
The balustrade was installed by Canterbury Balustrade to match preexisting. This was a glass and aluminum product.
Before
Formwork
Structural steelwork
Completed project
“S.C. Harris Builders recently built a deck for us, the team were ultra professional from design through to the end product which we are delighted with, they worked through the cold and rain in the middle of winter and despite being told by others that we couldn’t have it exactly how we wanted, they managed it no problem within a week. I highly recommend this business to anyone else considering a deck build or other renovation or building work.”
— Client Review (Caroline Knight)
Materials used
Kwila decking
This was used as it is a hard wearing, durable and stable timber that performs well in different weather conditions. As it is a dense hard wood it has little movement and shrink back and it ideal for outdoor use with a high lifespan.
Structural steel posts and beams
These were chosen as they can span greater distances than timber and were required to achieve one set of posts on a flat section of the site, rather than excavation of a secondary row of posts located in the middle of the deck, that would require deeper excavation due to the slope of the section in this location.
Stainless steel screws
These were used as they have greater holding power than nails, the stainless is resistant to rust and corrosion. The style of screw selected has a countersunk head, to achieve a flush finish with the decking boards. They were required on this project due the site being located in a sea spray zone.
Biggest challenge for the project
Supply chain issues
Due to a supply chain issue, the final earthquake brace couldn’t be installed due to the product not being available.
How we solved it: This required constant communication with the steel manufacture to ensure this was installed as soon as the product was available in the country.
See more examples of this work on the Decks page